Making Dolly Track
In the 60's I built my first portable dollies using ball bearings at 90 degrees
on pipe track. For sound I tried wheels flat on the top of pipe and idler wheels
to keep the dolly on the track. I didn't come up with the skateboard wheel idea
for sound. I think Pat O Mara Jr. might have. It has become a standard. I like
track wider than 2 foot Elemack track in the field and on dirt. It's more stable,
easier to level and can be made in longer lengths that reduce the number of
joints.
When we were making and selling track we used mahogany for ties not considering
that we were cutting down rain forest trees to get it. Mahogany is an ideal
wood as it is light, doesn't warp and low grade varieties were cheap. Seasoned
Douglas Fir will work fairly well. It would be nice to find a substitute for
mahogany or any of the threatened woods.
We and others track builders tried metal ties, but they don't work as well in
the dirt and with wedges. (See Nesting Apple
Boxes)
Sections of pipe or tube and even PVC pipe will work without ties on flat surfaces,
but don't try them on dirt or uneven surfaces. It is very difficult to level
the track.
When laying track it does not have to be perfectly level side to side, but should
be laid out in so it lies in a plane. On a slope one side can be a couple inches
lower. One person can "eye ball" it into a plane from one corner as others wedge
it up to level or in a plane. Use wedges or boxes under each tie and not a plank
under many ties to raise one side. You want separate support under the end of
each tie. If you are working with a crew that is used to leveling track with
a level, don't fight them with your own different method. It will take longer.
Shingles work well on stage for smaller adjustments. Place wedges or shingles
under the ties to avoid stepping on them.
Circular Track
Tom Ramsey the key grip got me going on circular track. We ended up with radii
from 4 feet to 60 feet. The longer radii are hard to set up with long lenses.
They need a very solid base and to be perfectly level. Joining large radius
track for long lenses is also tricky. Small bumps show up more on long lenses.
I stepped my radii out so that each outside track was the same radius as the
next inner track. So except for the outside two tracks, two pipes were bent
to the same radius. In a fixed set up the middle tracks could be eliminated
and the outside of one #1 track could work with the inside track of #3 Etc.
Label each track and make a diagram of radii and dimensions. It will help in
planning what track will fit in a location.
The beauty of circular track is a subject in the middle of the radii stays in
frame and in focus making it much easier for the operator. Moving super close
ups are possible.
To go from curve to straight the dolly trucks have to turn and change gauge
(track width) easily.
For one-time situations on a flat floor that you can screw into or where you
can put a floor down that you can screw into, consider 1" PVC screwed on radii
drawn from a center point. You can't do this on the dirt or uneven surfaces.
You can also curve PVC pipe with a rope and get approximate circular sections.
Try this before committing its possibility to the director. 1" PVC works.
Making aluminum track.
Get together with others who want track to pool resources and skills. Cut notches
in 2" x 4" x 36" wood ties. Cut them accurately on a large table saw or radial
arm saw. Make them all identical. Bill Bennett says the Hollywood gauge is 31-3/4
inches. I started at 32". Round the edges, drill two holes 5/16" center of where
the pipe goes and countersink the holes on the bottom side. Paint the ties with
a good exterior paint, varnish or sealer.
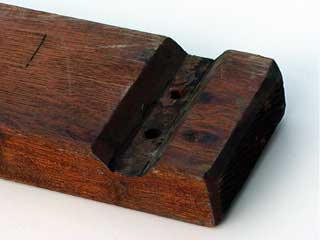
Dolly Track Tie
Note: these 45-degree cuts are shallower
than necessary. If you cut them closer to vertical they will be easier to cut.
Cutting at 45 degrees is hard to do consistently even on pretty big saws.
1-1/2" IPS Schedule 40 Aluminum Pipe 6061-T6 Alloy is the best. It comes 20
feet long and can be ordered from the mill in longer lengths in 2000 lb. orders.
That's about 40 pieces of 20 foot track. It gets really cheap this way. 1-1/2"
pipe has an outside diameter of 1.900" or 1 and 7/8".
Don't buy 6063-T3 hand railing pipe. It's too soft. So is rigid aluminum conduit.
If you find long enough lengths of other tube around this size it could be OK,
but would not be standard. I have used 1-1/2" and 1-1/4" EMT electrical conduit
on location, but it comes only 10 feet long and you need more joints. You need
galvanized 3/8-16 flat head screws about 2" long to join ties with pipe.
To assemble track, lay extra ties under the pipe to help stabilize it. Make
sure the two tracks are square with a large square or two squares so they line
up straight when two are joined. Use three electric drills to save changing
bits. One drill has a 5/16 drill to drill through the pipe with the hole in
the tie as a guide. The second slow speed reversible drill has a 3/8" x 16 tap
for tapping the wood tie and into the pipe. Kneel on the tie as you drill and
tap to align the ties. A third slow speed drill with a screwdriver bit will
screw in the screws. A carpenter's brace with a large screw bit will tighten
the screws when all four are in. Drill, tap and screw one screw on one end of
a tie then one on the other end. Go back to the first end and then to the last
on the other end. Tighten all with carpenter's brace or large screwdriver and
crescent wrench before moving to the next tie.
Note: To make the 3/8" - 16 tap stay in the drill chuck better, tighten two
nuts on the tap. Hold it in a vice and sand 3 flats with a hand sander by rotating
it 120 degrees each time. This can also be done on a stationary belt sander
using a coupling nut to index the tap. Put a bolt in the opposite end of the
coupling nut to make it stay put. Another way: Handles can be removed from tap
wrenches and the tap wrench will fit in some 1/2" drill chucks.
Track couplers are made of 1" x 1/2" aluminum bar stock. Drill 5/16 holes every
4 inches starting at 2 inches from one end. Tap the holes with a 3/8"-16 tap.
Use taping fluid. Make matching bars with 1/4" inch deep 3/8" holes. Don't cut
them apart until all operations are done. If they are held together with a piece
of 1-1/2" thin wall tube they stay together and are easier to use. Drill a 3/8"
bolt hole in the middle of each 4" section and cut it long wise 90 degrees from
the bolt hole so it can expand . Notches have to be filed in the ends of each
section of track to allow the coupler bolt clearance. File the notch at about
4 or 5 O Clock to miss hitting the dolly wheels and still clear the floor.
Care of aluminum track. Don't let the track get driven over, flat spots worn
by metal roof racks or other equipment, weathered, drug around on concrete,
or used as pry bars. We have used them for ladders and rigged from them, but
treat your track well.
You can move track in or out by pushing lighter weight dollies to one end of
a track and pulling the other end toward your goal. Remove the wedges first.
Push the dolly to the other end and repeat.
Around Hollywood this track is called Dexter Track. Fisher and Chapman have
adapters for some of their dollies for this track as many grips have it. This
track is called other things in other locations. You might check their gauge
if you are making some so yours will join theirs.
© Copyright 1999-2004 Ron Dexter. All Rights Reserved.